At Legacy Overland, we're not just about full restorations; we're about giving classic vehicles a new lease on life. When a Mercedes-Benz GD250 arrived at our workshop with a blown engine, we knew it was time to roll up our sleeves and perform an engine rebuild that would bring back its power and performance without undertaking a full restoration.
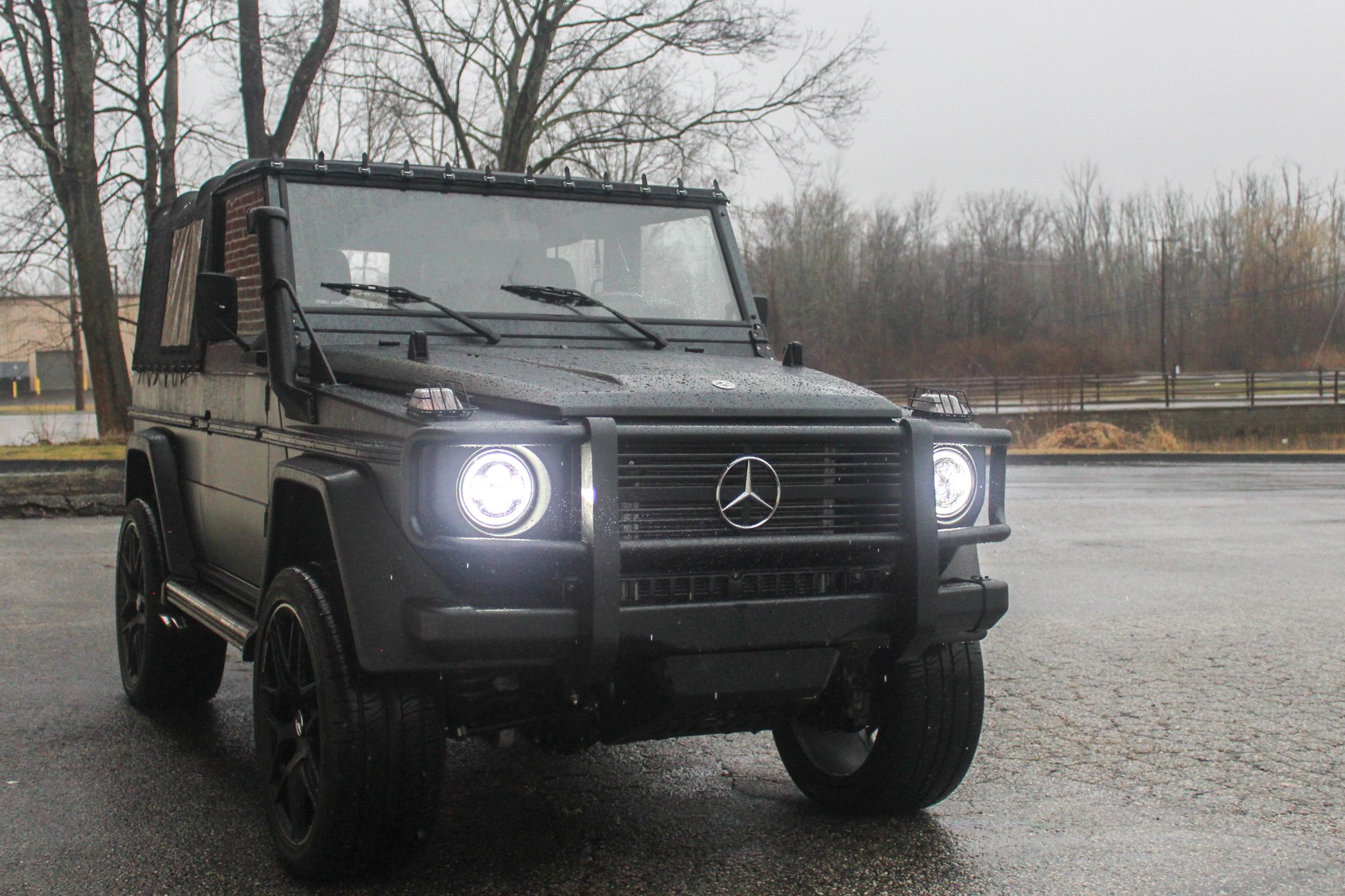
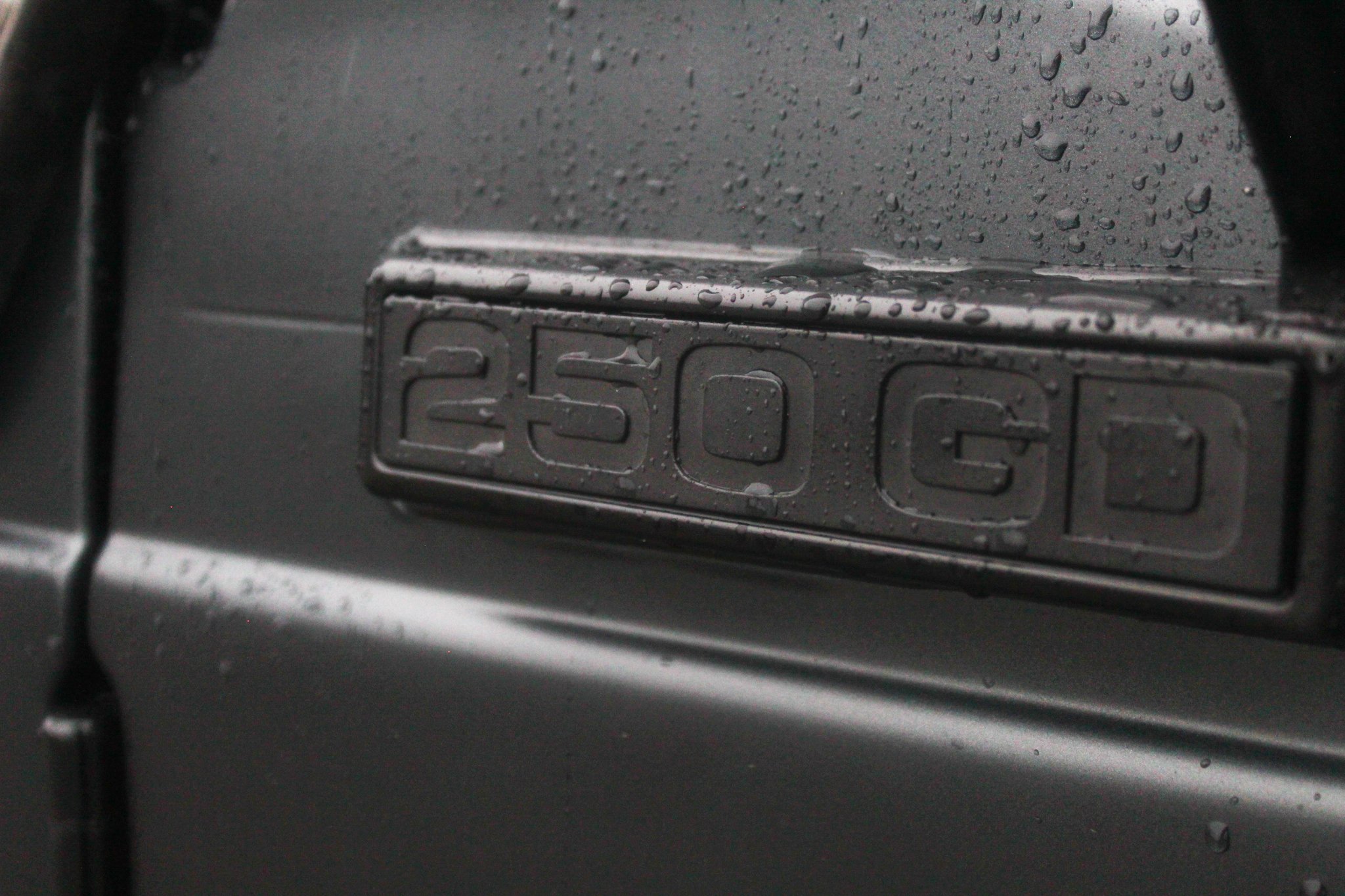
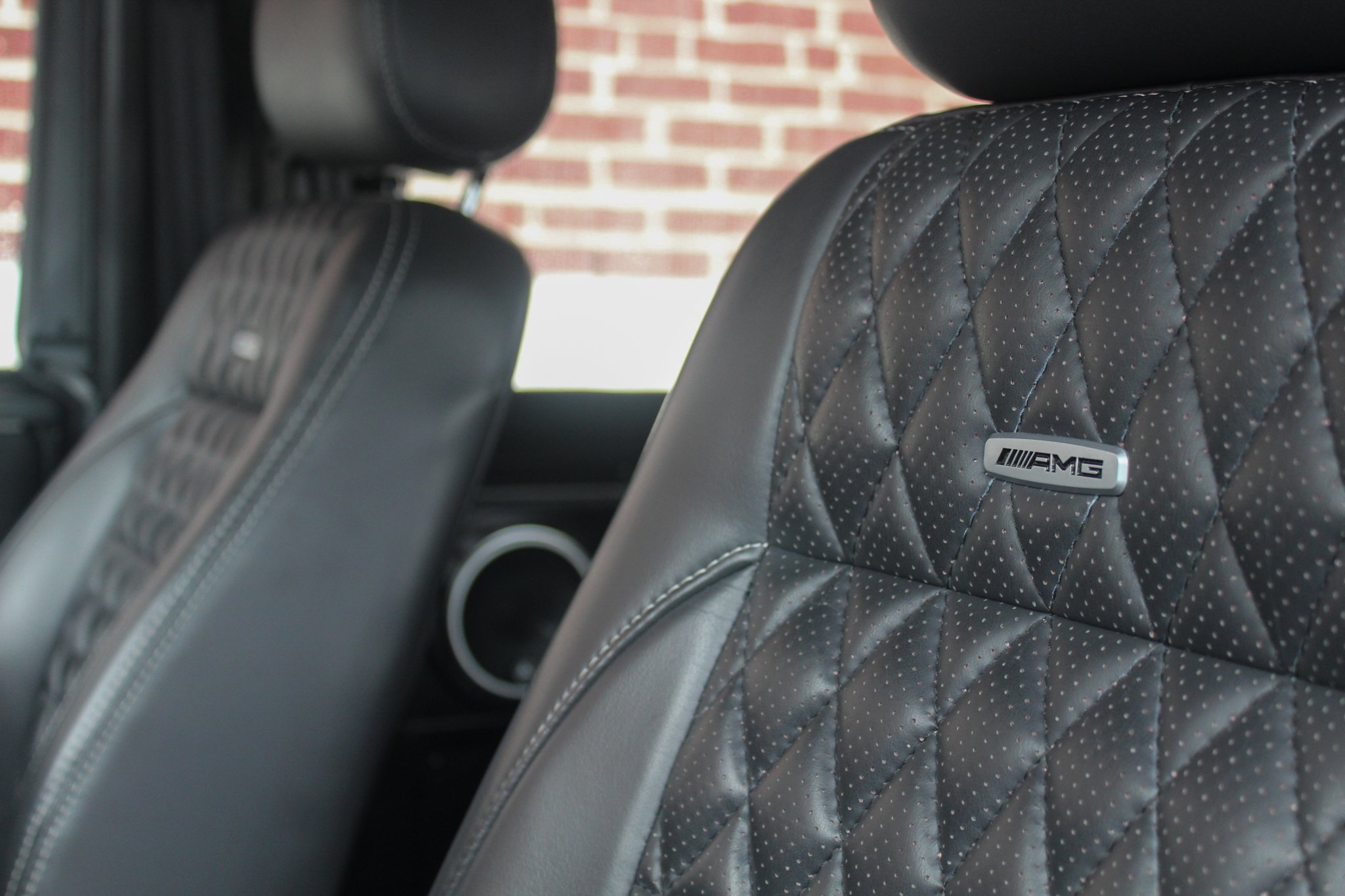
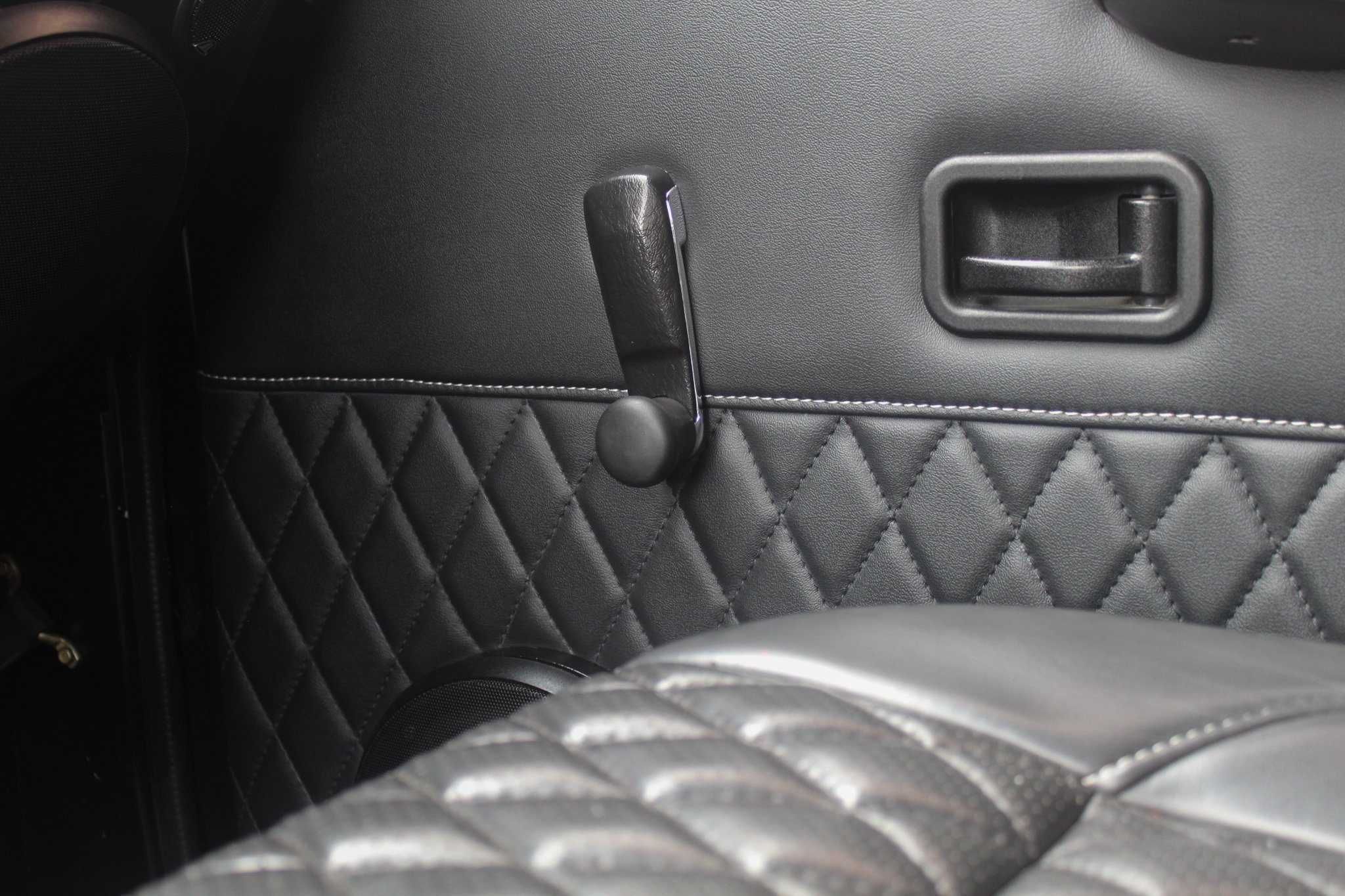
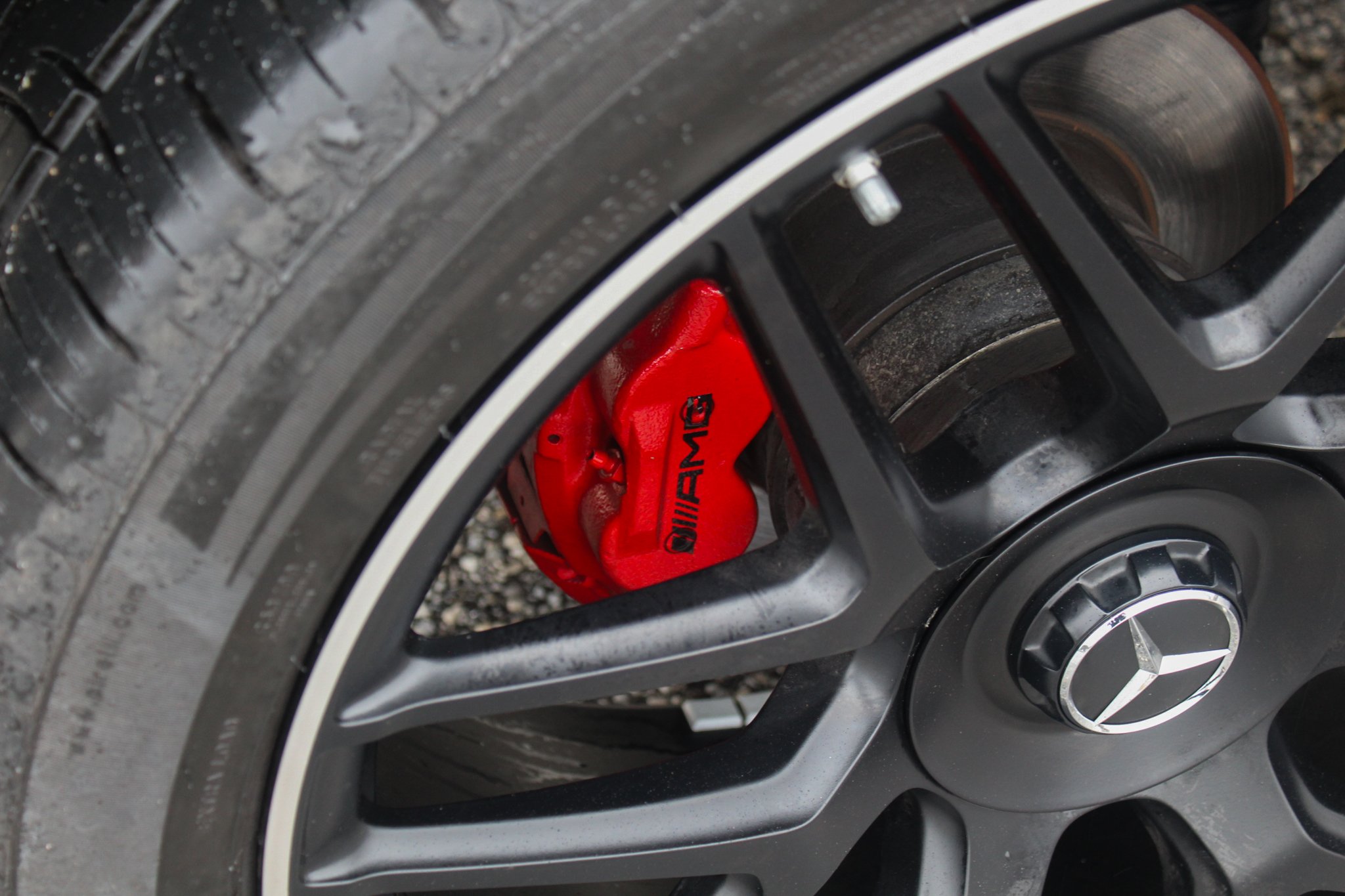
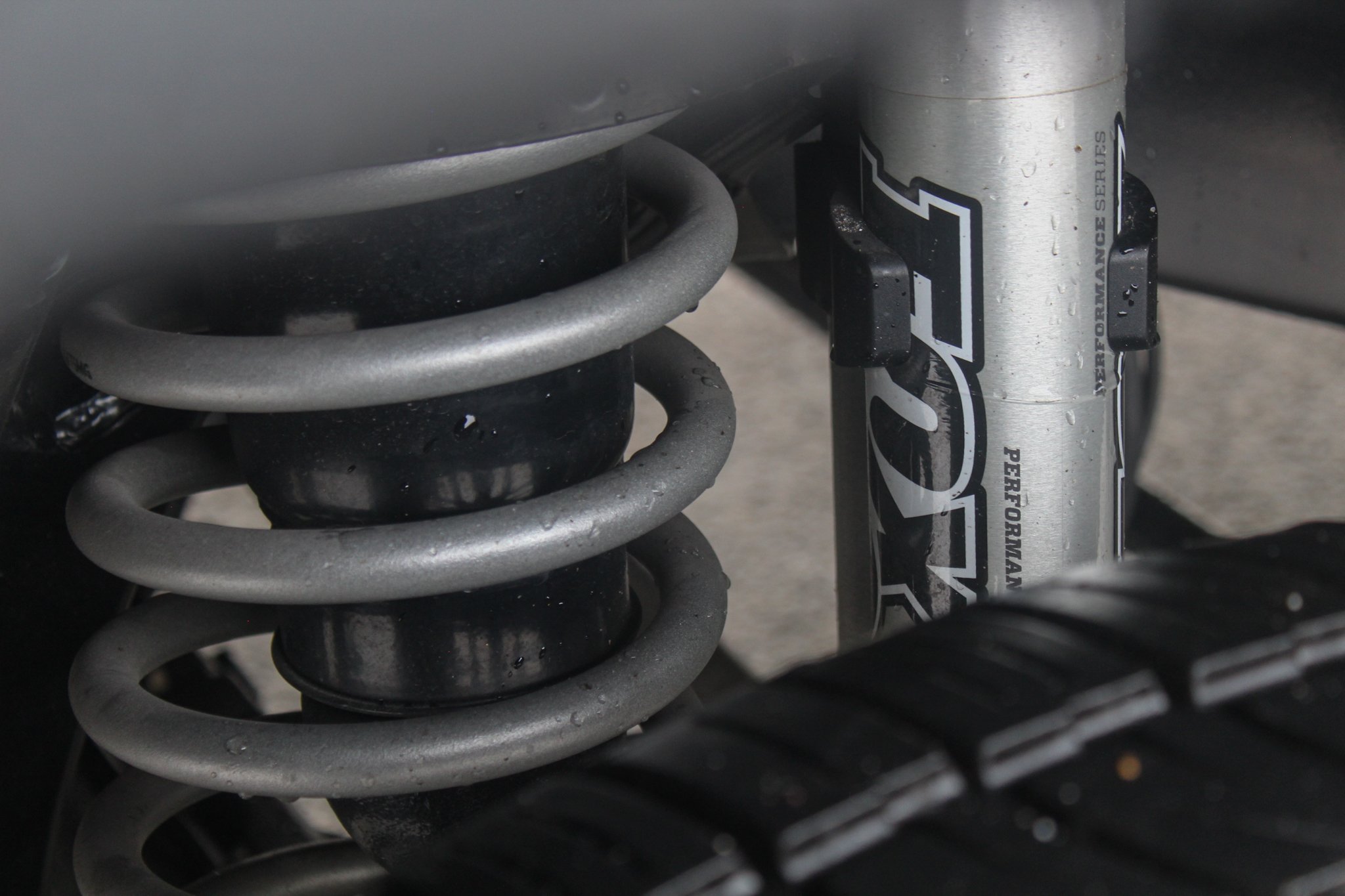
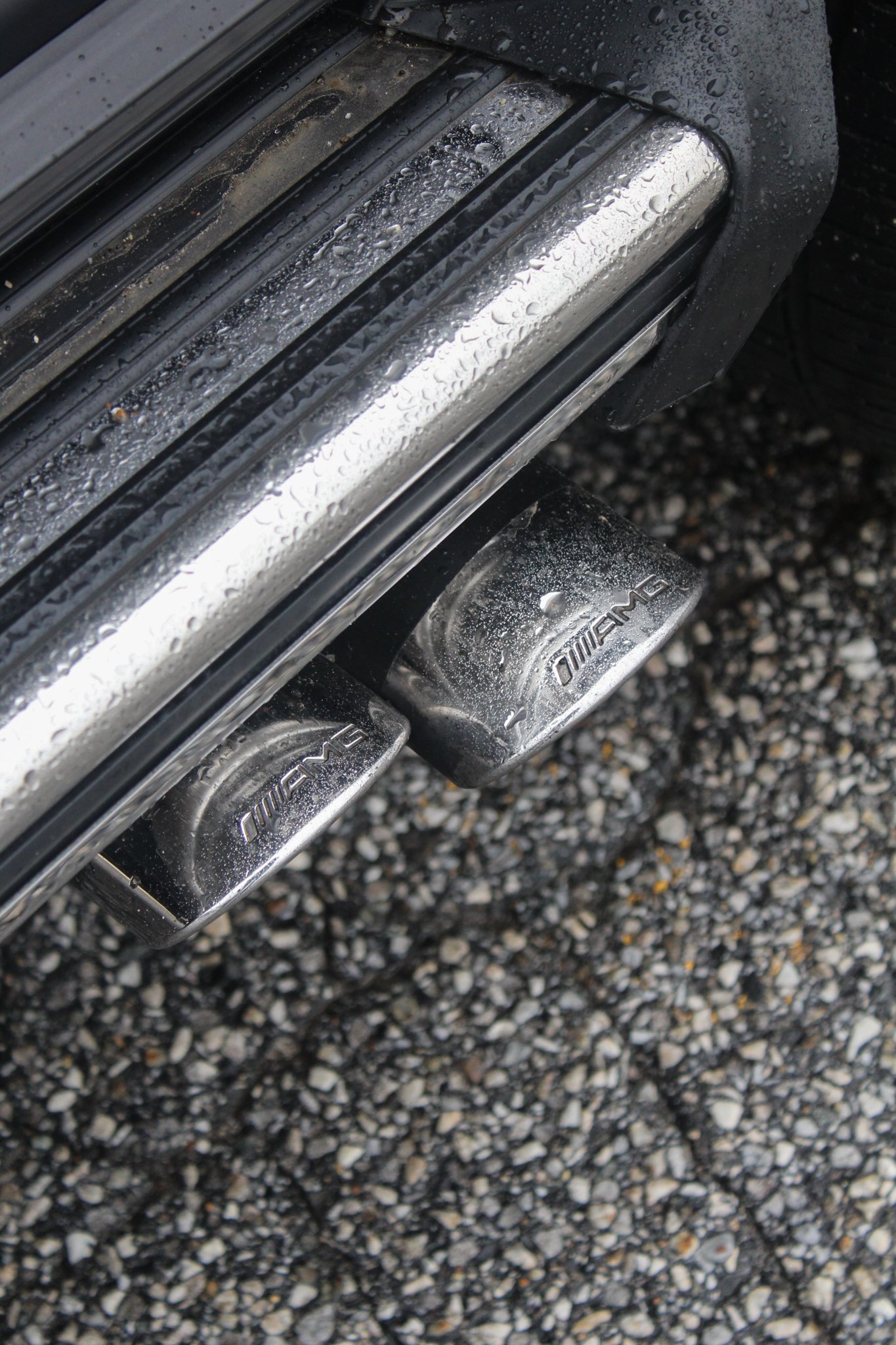
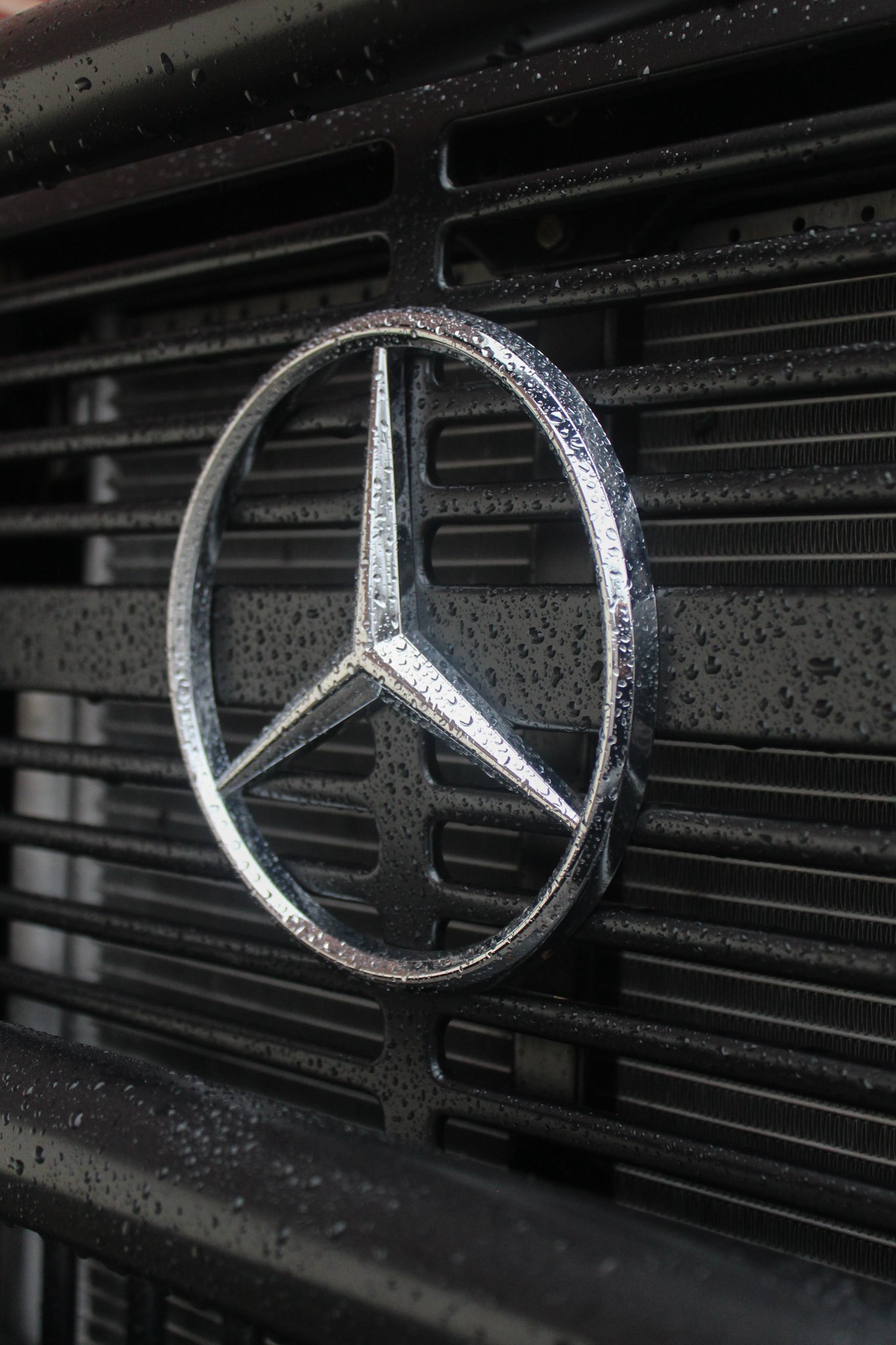
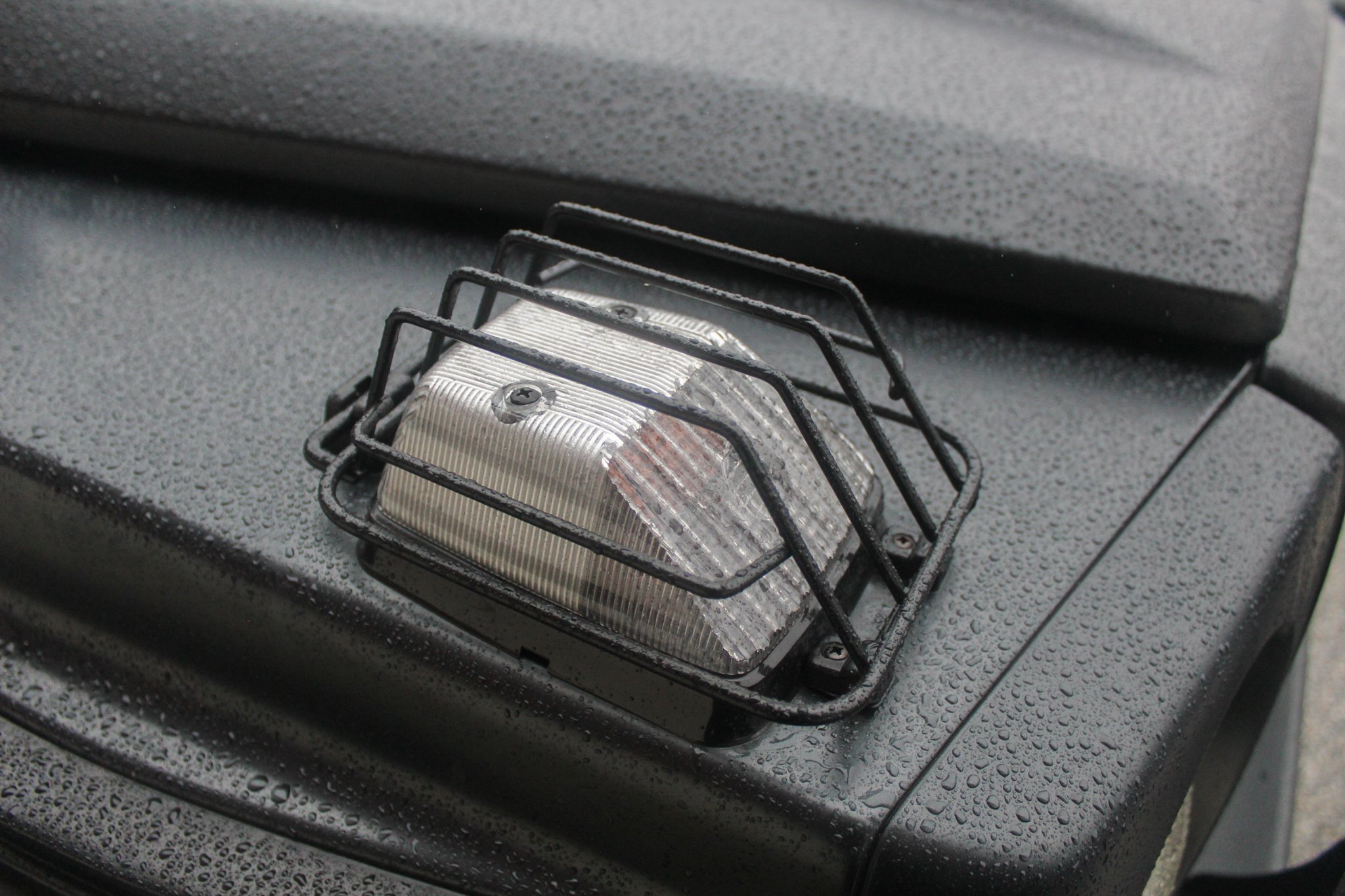
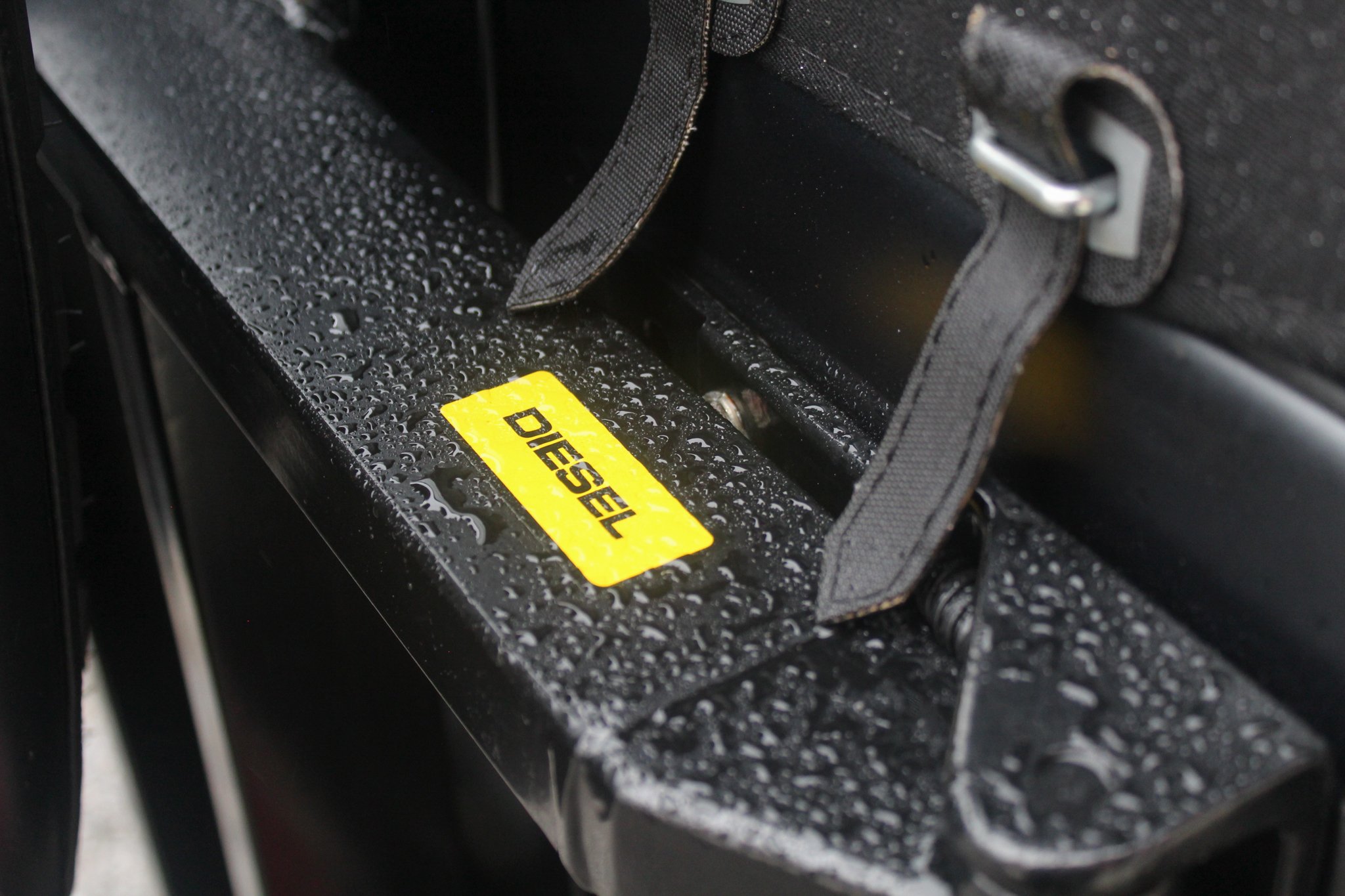
Assessing the Damage: Diagnostics and Breakdown
Our journey with this Mercedes began by diagnosing the extent of the damage to its heart, the OM605 turbo-diesel engine. Through comprehensive diagnostics, we pinpointed the issues plaguing this iconic powerplant. Once we had a clear picture, we meticulously disassembled the engine, delving deep into its internals to address the root cause of the problem.
Precision Revival: Machining and Enhancements
Precision was paramount in bringing this OM605 engine back to life. Machining services were employed to ensure every component was in perfect harmony with the diesel powerhouse. We meticulously ground and mag-tested the crankshaft, leaving no crack undetected. Cylinders were bored and honed to exacting standards, guaranteeing peak efficiency and power delivery.
During the rebuild, we spared no expense in upgrading critical components specific to the OM605. Forged i-beam rods and ARP rod bolts were installed to enhance durability under the diesel's torque loads. We opted for forged pistons and hardened wrist pins, ensuring they could withstand the rigors of high-performance diesel driving.
Reliability Reinforcements
Our focus extended beyond the engine to enhance the overall reliability of this Mercedes-Benz GD250. Turbo oil, water, and coolant lines specific to the OM605 were replaced to optimize turbocharger performance and ensure consistent cooling. A refresh of the cooling system with a new water pump and intercooler flush was crucial to maintaining optimal temperatures under diesel stress. We also made modifications to the A/C system for improved functionality, recognizing its importance in maintaining driver comfort during long hauls.
Electrical upgrades were seamlessly integrated, including Bluetooth functionality and a custom dual lock system for enhanced security. We even installed a custom door popper unit for added convenience during off-road adventures.
Finishing Touches: Attention to Detail
As the rebuild drew to a close, we turned our attention to the finer details specific to the OM605 and the Mercedes-Benz GD250. Manual window conversions were performed for simplicity and reliability, a hallmark of classic Mercedes engineering. Interior refinements included repairs to the amplifier cubby box and rewiring of the head unit for modern functionality without sacrificing the vehicle's vintage charm.
Exterior enhancements were also made to improve both performance and aesthetics. Charge piping was meticulously fabricated and painted wrinkle black, with a new intake snorkel installed to optimize airflow, specifically tailored to the OM605 diesel's needs.
A Timeless Rebirth
With unwavering attention to detail and a commitment to excellence, our engine rebuild of the 1992 Mercedes-Benz GD250, powered by the venerable OM605 turbo-diesel engine, brings together classic charm with modern performance. Every component, from the engine to the interior, has been meticulously restored or upgraded, ensuring a driving experience that transcends generations. At Legacy Overland, we take pride in revitalizing classic vehicles, preserving their legacy for years to come.
Some of the highlights include:
Complete engine dissasembly
Engine machining services were employed to match the block
The crankshaft was grinded and mag tested
Cylinders were bored and honed
Block decking performed
Upgraded forged pistons and hardened wrist pins were installed
Valve train maintenance included replacing glow plugs, valve seals, and guides
Forged i-beam rods and ARP rod bolts were installed
Bearing clearance was set to spec
OEM timing chain, chain guides, and tensioner were replaced
Turbo oil, water, and coolant lines were replaced
New water pump
Performed intercooler flush
AC controls wired to the firewall for improved functionality
Dual lock system installation
Custom door popper unit installation
Full alignment was performed
Replaced tie rod end
Exhaust system repair
Manual window conversion
Amplifier cubby box repair
Head unit rewiring
Fabricated charge piping was fabricated and painted wrinkle black
New intake installed to snorkel for improved airflow